ККД плюс
- ПОЧАТОК
- ЕКОТЮНІНГ-КІТ
- СуперАкваКар
- Пульс
- УПГ-2
- активатор Магнітний
- активатор Палива
- Впорскування води (ЕКОМАКС)
- ГБО
- NanoVit
- V-Tech box
- Екотопії
- AirWing
- антикор АКОР
- Рохер
- Екотюнінг Оіл
- ККД плюс
- Добавки FFI MPG
- Фільтри-нульовики (K & N)
- Емулятор лямбда-зонда
- Емулятор фільтр сажі
- Емулятор лямбда зонда і MAF
- корисності
- ФОТО
- КУПИТИ і КОНТАКТИ
Нова комплексна технологія
Нова комплексна технологія з метою значного поліпшення експлуатаційних якостей поршневих двигунів внутрішнього згоряння, вузлів і механізмів автотракторної техніки, авіації, на судах і кораблях, на тепловозах, на двигун - електрогенераторах.
Метод формування надтвердих поверхонь пар тертя, 14-го класу точності, з метою значного зниження шумів і багаторазового збільшення живучості машин, вузлів і механізмів на кораблях і плавзасобах ВМФ, для застосування на судах цивільного флоту затверджений «Дозволом Морського Регістру» м.Севастополь, а так само дозволений до застосування в промисловому секторі.
Завдання комплексної технології
Формувати надтверду, високоточну поверхню маталлические пар тертя в процесі експлуатації механізмів. Більш ніж в 1500 (тисяча п'ятсот) раз знизити коефіцієнт тертя в вузлах і механізмах. У десятки разів знизити пікові значення динамічних навантажень і запобігти наклеп в металі деталей пар тертя, а так само усунути кавітацію від механічних причин на стінках гільз циліндрів. Блокувати ефективно прорив газів через теплові зазори в замках компресійних кілець ДВС, роблячи компресію стабільно номінальної і не залежить від величини цих зазорів і температур. Збільшити крутний момент на низьких оборотах ДВС (у світовій практиці двигунобудування аналогів немає). В результаті значного поліпшення технічних і експлуатаційних параметрів, в цілому, категорично поліпшити показники екологічні.
За оцінками фахівців, застосування методу даної технології для ДВС і трансмісії автомашин КАМАЗ (кар'єрний самоскид) приносить значний прибуток за рахунок поліпшення Техноком-економічних показників роботи ДВС і механізмів:
- Зменшує витрату палива
- - При холостих обертах на 70-80%;
- - При малих і часткових навантаженнях на 30-50%;
- - При потужних режимах на 20-35%;
- - В середньому до 40%;
- Збільшує крутний момент на низьких оборотах на 20-25%;
- Підвищує потужність ДВС на 25-35%;
- Знижує витрату масла на чад на 95-98%;
- Забезпечує збільшення ресурсу ДВС без капремонту до 10 разів;
- Знижує коефіцієнт тертя в вузлах і механізмах в 1500 (Одна тисяча п'ятсот) раз .;
- Гарантує від зносу при «Холодному запуску» протягом всього терміну експлуатації;
- Значно знижує шум і вібрації;
- Нормалізує і стабілізує компресію протягом усього терміну служби поршневої групи ДВС .;
- Гарантує легкий запуск ДВС при мінусових температурах;
- Значно покращує екологічні показники (по тепловому забрудненню в тому числі).
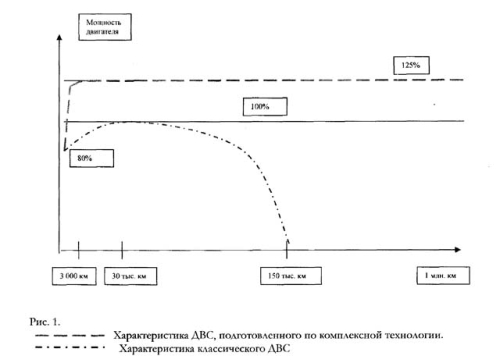
Модернізований за даною технологією новий або оновлений ДВС проявляє наступні характеристики:
- - До 3 000 км пробігу поліпшення характеристик до «сверхнорм»;
- - Від 3 000 км до 1,5 млн. Км пробігу стабільне утримання досягнутих характеристик.
Практика нормативної експлуатації вітчизняних ДВС в цілому свідчить: до 30 тис. Км. пробігу двигун працює все краще і краще, від 30 тис. км. до 70 тис. км., з причин тертя він починає поступово зношуватися і в кінці цього терміну бажано поміняти кільця. Далі ДВС зношується необоротно і до 150 тис. Км. пробігу потребує капітального ремонту з повною заміною циліндропоршневої групи. Комплексна технологія запобігає зносу від тертя протягом заявленої норми моторесурсу, а також робить компресію незалежної від теплових і потужних режимів ДВС. Навіть "поважний" по всім поняттям двигун і в кінці моторесурсу працює як і раніше бездоганно, малошумний, постійно потужно і бездимний, коли в ньому працює система комплексної технології.
Характеристики потужності, витрати палива і масла при системі комплексної технології
Відомо, що: чим менше зазор в гарячому стані між головкою поршня над першим (вогневим) кільцем і циліндром, тим більше дросселирование газу в цьому зазорі і кращі умови роботи кілець. Так при зазорі 0,05 і температурі газу в верхній частині зазору 800 градусів С, вже на відстані 20мм від верхньої частини температура газу знижується до 400 градусів С, а при зазорі, що дорівнює 0,5 мм - лише до 700 градусів С. Тиск газу на поршневі кільця змінюється як від відстані до кільця так і від тиску газу в циліндрі. Якщо прийняти тиск в циліндрі ДВС автомобіля за 100%, то тиск, що діє на I кільце складе - 75%, на II - 17%, а на III - 7% (при номінальних зазорах).
Запобігання прориву газів в картер, як видно, забезпечується зниженням тисків в результаті дроселювання газу при проходженні тунелів лабіринту і зазорів, утворених кільцями, що становить витратну частину і є неефективним витратою енергії розпечених газів в циліндрах двигуна. На сверхтіхоходних суднових двигунах, для запобігання прориву газів в картер, особливо при проходженні поршня району ВМТ на малих обертах під навантаженням, встановлюють до семи компресійних кілець (зрозумілий так-же питання тертя).
Система комплексної технології конструкційно блокує газ на рівні верхнього (вогневого) кільця і незалежно від величин зазорів кілець ефективно повертає на колінвал до 24% енергії вибуху в камері згоряння ДВС автомобіля. Таким методм забезпечуються показники по збільшенню крутного моменту на "низах", збільшення потужності, скорочення витрати палива і масла (на угар), а в цілому - визначаються екологічні показники рівня Європейських норм протягом усього терміну експлуатації.
Живучість ДВС для спорту, моторесурс 1000000 км. серійного ДВС
При значному форсуванні двигуна підвищені навантаження в підшипниках КШМ можуть привести до руйнування масляного клина в ньому, тобто до підвищених износам підшипника, схоплюванню металів, виплавлення підшипника і т.д. Навантаження на підшипник залежить, як від окружної швидкості підшипника, яка визначає величини тертя, так і від розмірів: довжини підшипника і його діаметра при даному тиску на поршень. Енергетичні витрати на подолання сил тертя в основних вузлах ДВС складають: ЦПГ - 11,5%; ГРМ - 2,7%; кривошип - 3% від потужності автомобільного двигуна. Комплексна технологія, на відміну від інших методів форсування ДВС, знижує коефіцієнт тертя в 1500 разів, а в цілому - збільшує потужність ДВС на 25-30%, утримує геометрію деталей і в результаті оптимальний розмір зазору «поршень-циліндр» весь період моторесурсу, і своєї ефективністю дозволяє установку компресійних кілець з збільшеними тепловими зазорами. Доцільно збільшити на 0,2 мм від номіналу, зазор верхнього (вогневого) кільця з метою перерозподілити тиск і температури, тим самим значно пом'якшуючи умови роботи компресійних кілець і для запобігання теплового клину ЦПГ при перегріванні ДВС. Такі можливості комплексної технології.
Можливо містити ДВС в стабільно-ідеальному стані, повторюючи Бернадський відновлення механізмів через 150 тис.км. пробігу (300000 км. для високотехнологічних ДВС) і т. д. Застосування комплексної технології універсально вирішує завдання 1 млн. км. пробігу і вище, для нового ДВС.
Поліпшення параметрів роботи авіаційного поршневого ДВС
Теплові зазори поршневих кілець виконуються з урахуванням умов від теплового заклинювання при форсованому режимі роботи ДВС. Авіаційні ДВС на граничних потужних режимах витримують значні навантаження по тепловому потоку, які можуть досягти величини 2500 градусів. Тому набір великої висоти проводиться поетапно за кілька підйомів, з метою зберегти ДВС від теплового руйнування. При зменшенні навантажень - номінальному, середньому, малому - потужних режимах, тепловий потік зменшується і, як наслідок, це визначає помітне збільшення теплових зазорів поршневих кілець, що призводить до прориву газів в картер і втрати потужності в добре підготовленому поршневому двигуні. При цьому через збільшені теплові зазори поршневих кілець масло з картера потрапляє в камеру згоряння. Під час стоянки, коли ДВС не прогрітий, з нижніх циліндрів, через теплові зазори поршневих кілець так-же відбувається істотна втрата масла (замаслений грунт на стоянці, рульових доріжках). Застосування комплексної технології дозволяє блокувати ефективно прорив газів в картер і втрату масла, що відбуваються, як наслідок, від збільшених в стандарті теплових зазорів поршневих кілець авіаційного ДВС.
При роботі поршневого ДВС тепло від поршня відводиться: 20-25% - через масло в картері і 75-80% - контактно - поршень -> кільця -> циліндр. У добре підготовленому ДВС, через зубчастості мікрорельєфу поверхонь пар тертя, від 100% геометричній площі контакту деталей, реально стикаються 3 (три)% площі, а в зношених ДВС ( «бочка», еліпс в циліндрах) і цього менше. Даний параметр категорично визначає межу щільності теплового потоку відводиться від поршня до стінки циліндра. Застосування комплексної технології формує плавно-хвилястий профіль поверхонь пар тертя 14 класу точності і створює пляму реального контакту рівного 16 (шістнадцять)%. Збільшення понад п'ять разів площі реального контакту збільшує можливість відведення тепла, що захищає поршень, кільця, і масляний клин від перегріву. Така поверхня деталей пар тертя характеризується деякими властивостями: аномально низький коефіцієнт тертя, сверхтвёрдость, міцність, тримає геометрію деталей, висока зносостійкість, висока теплопровідність, предотврощает утворення оксидів азоту (NOx) в целиндра знижуючи на 80-90 %% їх кількість, не піддається корозії , діелектрик, витримує температуру 3500 градусів С. Гарантує поверхню від теплового руйнування при Форсаж.
Усунення кавітації на зовнішніх стінках циліндрів і умов «наклепу» в металі пар тертя
Вібрації гільз циліндрів при навантаженнях формують порожнини розрідженого в охолоджуючої рідини, де утворюються кавитационні бульбашки, при схлопуванні яких в мікрозонах виникають тиску до 600 атм. і температура до 1200 градусів С (мікровибух) і з зовнішньої поверхні гільзи виламуються кластери (мікрочастинки) метала, утворюються мікротріщини, а потім - розрив поверхні.
Система комплексної технології миттєво перерозподіляє енергію пружної деформації в металі пар тертя, в десятки разів знижуючи пікові значення, тобто вібрації стінок циліндрів згладжуються і кавітація запобігається. Так само миттєво усуваються критичні деформаційні моменти кристалічної решітки, що утворюють «наклеп» в металі пар, що труться вузлів і різних механізмів (ДВС, редукторів, КПП, ШРУС і т. Д.).
Переваги застосування комплексної технології на дизелях і дизелях з наддувом, а також бензинових ДВС при запусках
Складнощі пуску при низьких температурах добре відомі. Найбільш складною для вирішення є проблема самозаймання палива в дизелях. Низька початкова температура заряду, а у наддувних двигунів - до того ж низька (Е) ступінь стиснення, не забезпечують отримання досить високої температури стиснення. Холодні стінки циліндрів відводять тепло від стисненого заряду, а зазори в замках компресійних кілець можуть звести нанівець компресію, катастрофічно знижуючи його температуру. При ступені стиснення 13 (дуже низькою для атмосферного дизеля і досить високою для дизеля з наддувом) температура стиснення досягає 630 градусів С на режимі повного навантаження, але значно нижче, на режимах часткових навантажень, коли турбокомпресор має малу або навіть нульову продуктивність. Дизель без наддуву в тих же атмосферних умовах при ступені стиснення 16 забезпечує отримання температури стиснення, що дорівнює 720 градусів С. Очевидно, що у дизеля з наддувом на режимі пуску компресор не працює, і в результаті температура стиснення виходить дуже низькою.
Застосування комплексної технології робить компресію незалежної від величини зазорів в замках компресійних кілець і забезпечує надійне підвищення температури стиснення, необхідної для успішного запуску дизеля. Запуск звичайного бензинового двигуна можна назвати легким і безпроблемним, але за рахунок збагачення суміші для пуску і прогріву (при цьому відбувається перевитрата палива в 2-3 рази, екологічно брудний вихлоп, низька потужність ДВС). Застосувавши комплексну технологію, зазначені недоліки в значній мірі усуваються, так як в збагаченні суміші для пуску і прогріву необхідності практично немає.
Коментарі
Коментуючи, пам'ятайте про те, що зміст і тон Вашого повідомлення можуть зачіпати почуття реальних людей, проявляйте повагу та толерантність до своїх співрозмовників навіть у тому випадку, якщо Ви не поділяєте їхню думку, Ваша поведінка за умов свободи висловлювань та анонімності, наданих інтернетом, змінює не тільки віртуальний, але й реальний світ. Всі коменти приховані з індексу, спам контролюється.